With its modular wooden wind turbine towers, Modvion aims to deliver a high-impact product to the energy industry. In parallel with its industrialisation journey, it is leading a BioInnovation project addressing key details to enable more widespread bonding of wooden towers in the field. The results pave the way for the bonding of more advanced wooden structures.
Since time immemorial, people have used the wind as a source of energy – just think of the landscapes of old, where windmills were an intrinsic part of the landscape. So when Modvion – a manufacturer of wooden wind turbine towers – is asked if their idea is unique, there is no simple answer. The principle of building wooden structures that capitalise on the wind is certainly old, but when it comes to doing it in this updated way, they are quite unique. Instead of the typical steel or concrete structures, the product leaving Modvion’s factory is made from renewable laminated spruce wood from Finland. Their towers are delivered in modules and assembled on site.
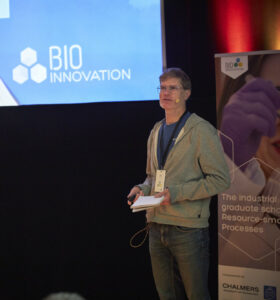
Jonas Wranne, Modvion. Photo: Johan Olsson
With support from BioInnovation, Modvion is now leading a project that also includes RISE and the chemical company Henkel. Together, the stakeholders are developing the adhesive that bonds the various parts of the tower together, as well as a developing a methodology for bonding in the field – an approach that is currently lacking in the construction industry.
– A bonded structure requires significantly less maintenance than today’s structures, which have as many as 50 000 bolts that have to be tightened every year. It is an financially competitive alternative that also provides environmental and climate benefits, says Jonas Wranne, Development Engineer at Modvion. The carbon dioxide emissions from the wooden turbine tower bind more carbon dioxide than it generates during production, enabling net-zero wind power, and once worn out, the tower can be recycled into glulam beams for the construction sector. The product life cycle of the wood raw material is more than 100–150 years.
Aiming to enable large-scale bonding outdoors
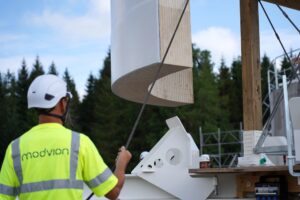
Photo: Modvion
Modvion already bonds its towers currently. But bonding requires a controlled climate and a controlled temperature. Therefore, one project goal is to develop the adhesive so that it will be able to cure at significantly colder temperatures.
– Carrying out bonding processes in the field is tricky, it is difficult to guarantee the conditions required to get a result of sufficiently high quality. So, what we’re doing now is developing a reliable process and ensuring that it is fast enough to work on a large scale. We aim to compile the results into a recommendation, to be used in future tower erection, says Jonas Wranne.
Smart method for more wooden structures
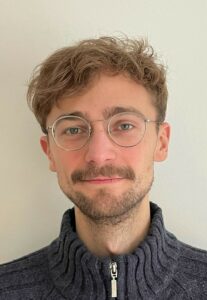
Viktor Norbäck, RISE. Photo: Private
In addition to contributing to Modvion’s ongoing industrialisation journey, RISE sees that the results can benefit the construction industry in general:
– Quality-assured methods for outdoor bonding is also applicable when building other types of wooden structures. The research done so far shows that adhesives can be a beneficial alternative with high structural performance, efficient production, and low maintenance costs. Our hope is that we can disseminate the results of this project to more companies in the construction sector, says Viktor Norbäck, research and development engineer at RISE.
Participants
Modvion AB, RISE (Research Institutes of Sweden) and Henkel & Cie. AG.
Budget & time plan
The project’s total budget is 6,8 MSEK and the project runs for 17 months – between August 2023 and December 2024.