Snart kan gamla pappersförpackningar bli till verktyg inom fordonsindustrin. Ett BioInnovation-projekt är först ut att 3D-printa verktyg för vakuumformning, tillverkade av återvunnen cellulosa. Materialet i kombination med tekniken kan minska plastförbrukningen och öppnar för nya cirkulära affärsmodeller.
I fordonsindustrin är det rusch efter lösningar som kan minska mängden plast, både i fordonen och på fabriken. Nu är ett BioInnovation-projekt först ut att 3D-printa återvunna cellulosafibrer till verktyg som används för att tillverka fordonsdelar genom vakuumformning. Det är verktyg som idag tillverkas av plast. Spillmaterialet kommer från Stora Ensos produktion av pappersförpackningar, och tillsammans med RISE och fordonstillverkaren Ecoist Cars utgör de projektets parter.
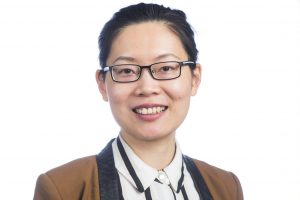
Ting Yang Nilsson, forskare RISE.
– Att 3D-printa verktyg av återvunnen cellulosa minskar fossilberoendet och gör både fordons- och förpackningsindustrin mer cirkulär. Vakuumformningsverktyg slits och måste bytas ut med jämna mellanrum, men idag är verktygen tillverkade av plast och kan inte återvinnas. Med den här lösningen kan vi återvinna verktygen till en likadan produkt och allt spill från produktionen går tillbaka in i tillverkningen, säger Ting Yang Nilsson, projektansvarig forskare på RISE.
”Enklare för fordonsindustrin att premiera hållbarhet”
I projektet har ett verktyg av den pappersbaserade kompositen använts för att tillverka tjugotalet komponenter till Ecoist Cars eldrivna trehjuling Tian.
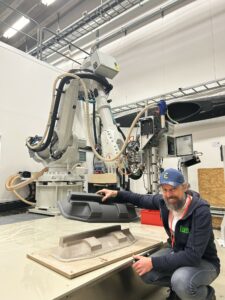
Thomas Koch. Foto: Rise
– Vi står för hållbarhet och då räcker det inte med att tillverka ett fordon som går på el, även materialvalen är jätteviktiga. På sikt kan det här materialet i kombination med tekniken göra det enklare för fordonsindustrin att premiera hållbarhet; verktyget av återvunnen cellulosa presterar lika bra som dagens verktyg, är återvinningsbart och finansiellt hållbart. Ett sådant alternativ har jag inte sett innan, säger Thomas Koch, grundare och vd Ecoist Cars.
Nu har fler svenska vakuumformningsleverantörer och tillverkare inom tunga fordon visat intresse för projektet. En stor fördel med 3D-printing inom just fordonsindustrin är att man slipper förvara verktyg till äldre modeller. Idag måste plastverktygen sparas för att reservdelar ska kunna tillverkas vid behov. En mer kostnadseffektiv lösning skulle istället vara att 3D-printa nya verktyg när det behövs.
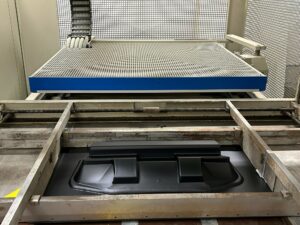
Formning. Foto: Rise
”Hållbarhet och affärsmässighet går ihop”
Stora Ensos förpackningar tillverkas av en blandning av återvunna och nya pappersfibrer. I projektet har parterna testat spillmaterial av både ny och återvunnen cellulosa med intressanta resultat. Det visade sig att just spillet av återvunnen cellulosa lämpade sig överlägset bra för 3D-printing. I nästa steg ska projektpartnerna bland annat undersöka om också konsumenters förpackningsavfall kan återvinnas för ändamålet.
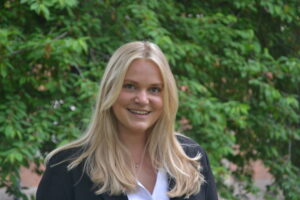
Annika Racki. Foto: Stora Enso
– Restmaterial är en värdefull resurs. Idag återanvänder vi produktionsspillet i nya förpackningar och det här skulle kunna vara ett sätt att upcykla det ytterligare. BioInnovation-projektet är extra intressant eftersom vi teamar upp med andra industrier och bygger nya värdekedjor där hållbarhet och affärsmässighet går ihop. Det tror jag är en framgångsfaktor, säger Annika Racki, Business Development Manager, Stora Enso.
- Verktyg och vakumformad komponent. Foto: RISE
- Thomas Koch, Ting Yang Nilsson och Annika Racki med verktyg. Foto: Rise